PVDC Latex Grades Overview
PVDC Barrier Coatings
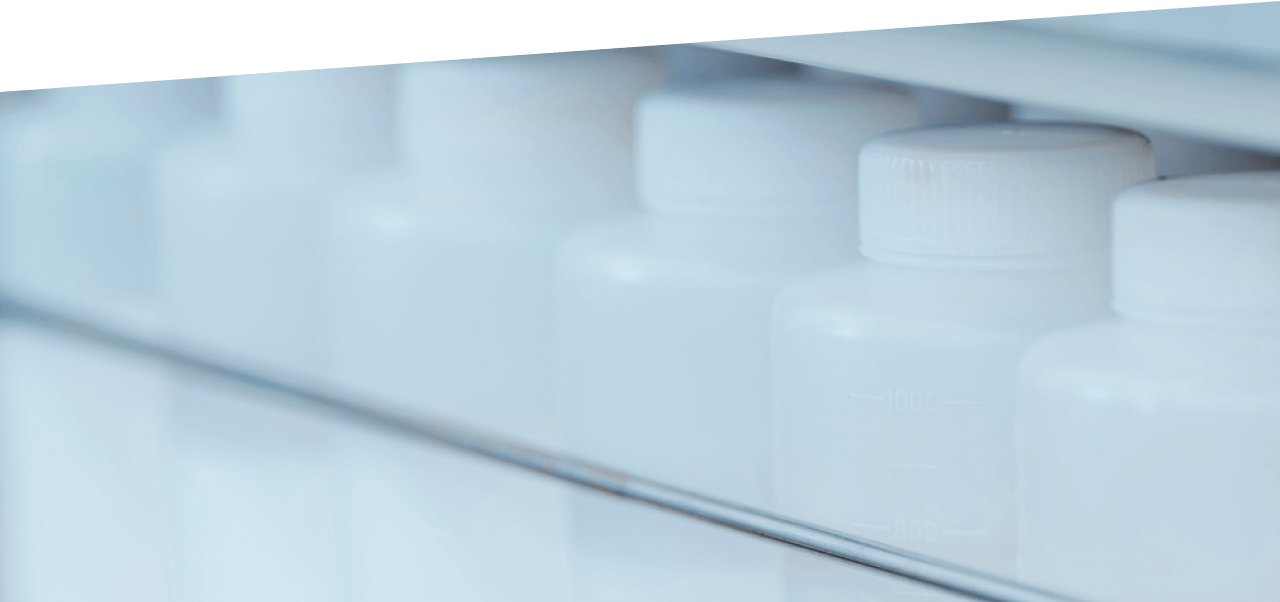
Representative Grades and Key Properties (For Export Only)
We offer a diverse range of high-quality PVDC Latex grades to suit various application needs. Contact us for more detailed information and assistance in selecting the best grade for your project.
Grade | Solid Content (%) |
pH | Viscosity (mPa・s) |
Surface Tension (mN/m) |
Water vapor transmission rate (g/m³・day) |
Oxygen transmission rate (cc/m²・day・0.1MPa) |
Application |
---|---|---|---|---|---|---|---|
L813D | 60 | 3.0 | 35 | 42 | 0.7 | 0.7 | Pharmaceutical Blister Packaging |
L818C | 60 | 3.0 | 42 | 49 | 0.7 | 0.7 | |
L818D | 60 | 2.9 | 29 | 50 | 0.6 | 0.6 |
- Note:
・Water vapor transmission rate was measured by the AK-S LTX Method (S-059) (38℃, 90% RH) - ・Oxygen transmission rate was measured by AK-S LTX Method (S-079) at 23℃, Dry
- ・PVDC Latex-Coated Film converted to reflect 30μm PVDC Layer Thickness
- ・Water vapor transmission rate was measured by coating an ONy substrate, and oxygen transmission rate was measured by coating an OPP substrate.
- ・The values provided here are typical averages based on laboratory testing and should not be considered product specifications.
- ・These measurements were conducted using our in-house AK-S LTX Method. These examples are not guaranteed.
- ・Not all grades are compliant with regulations in every country or region, and some grades may be discontinued without prior notice. For regulatory details, please contact us directly.
Packaging for
PVDC Latex Products
Our PVDC Latex is supplied in 1,200 kg Intermediate Bulk Containers (IBCs), offering efficient transport for large-scale industrial applications.
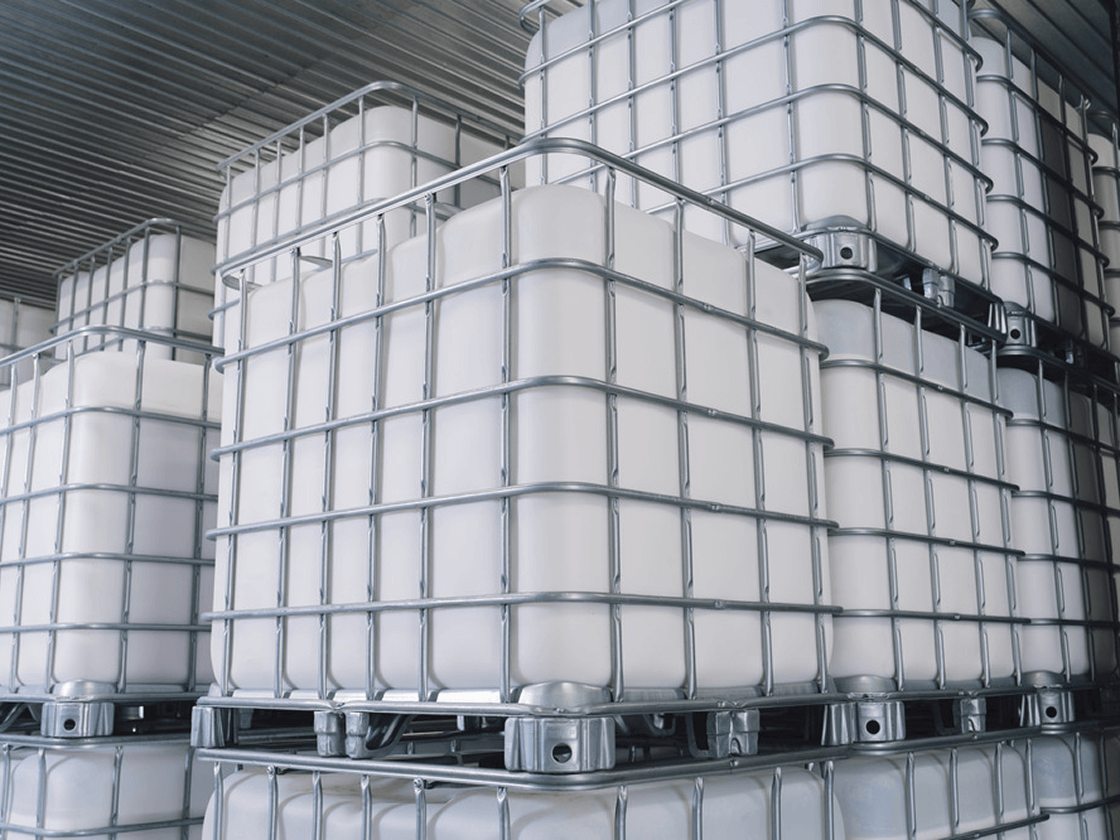
Comprehensive Safety Data Sheets (SDS), technical specifications, usage guidelines, and regulatory details are available upon request.
Not all grades are compliant with regulations in every country or region, and some grades may be discontinued without prior notice. For regulatory details, please contact us directly.
Application and Coating Methods
① About the PVDC Latex Coating Layer
- PVDC Latex is applied to a substrate, smoothed, and dried using hot air or infrared heaters to form a continuous PVDC film on the surface. Due to its water-based dispersion, significant heat energy is required to evaporate the water, making it essential to optimize temperature, humidity, airflow, coating thickness, and coating speed. This ensures an ideal environment for optimal film formation.
② Pre-Treatment
- Surface treatments like corona discharge and anchor coating (preferably polyurethane-based) are commonly applied for improved adhesion on plastic films.
③ Coating Methods and Precautions
- Various coating methods are compatible with PVDC Latex, including air knife, reverse gravure, and Mayer bar.
- Drying the coated film involves initially setting lower temperatures in the dryer to prevent skinning, gradually increasing toward the end (e.g., 100℃ at the beginning, rising to 110–120℃). In cases where curling occurs after coating, moisture control may be necessary.
Examples of PVDC Latex Coaters
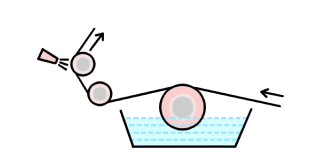
Air Knife Coater
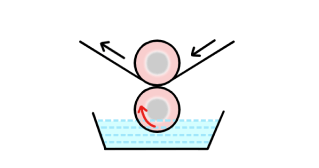
Gravure Coater
④ Post-Coating Handling
- Additionally, anti-blocking agents (e.g., silica or wax emulsions) can be added to prevent layers from sticking during winding
Maximizing PVDC Latex
Coating Performance
Two key steps are critical to optimize the performance of PVDC Latex coatings: ①Film formation and ②Crystallization.

①Film Formation
Ideal hot air conditions (temperature, humidity, and airflow) in the drying oven ensure optimal film formation by maintaining the correct temperature for the latex solution.
②Crystallization
Proper heat treatment enhances crystallization, smoothes the coated film surface and prevents blocking. Be mindful that the performance of the PVDC coating may decline if aging or crystallization temperatures are too high or too low.
- Note on aging: Aging, or exposing the coating to higher temperatures (e.g., 40℃ for 48 hours), is recommended to enhance PVDC polymer crystallization.
Handling Precautions for PVDC Latex
Always consult the Safety Data Sheet (SDS) for the specific grade you are using, wear appropriate protective gear, and adhere to all safety guidelines.
- Coating Conditions
Temperature and time affect the crystallinity of PVDC Latex, significantly impacting coating conditions and film properties. Proper inventory management, coating condition monitoring, and aging control of coated films are essential. - Storage
Keep containers tightly sealed to prevent skinning. Store in a cool, dark place, avoiding freezing temperatures (below 3℃) or high heat (above 30℃). Use within the specified shelf life. High temperatures can cause hydrochloric chloride release which leads to pH reduction and coagulation, affecting product quality. - Expiration
Check the expiration date for each grade, as it may vary. - Transfer and Mixing
Avoid using high-shear pumps that may cause coagulation. Use low-impact transfer methods, such as gravity or air pressure. - Foam Management
Avoid high drops or rapid stirring to prevent foaming. Position outlets near the bottom of containers and install an approximately 100-μm filter before coating. If the foam dries before it completely disappears, it may become a powdery aggregate and be mixed into the latex. - Equipment and Materials
PVDC Latex is acidic. Use compatible materials like polyethylene, PVC, epoxy-lined metals, FRP, or stainless steel (SUS 316) for tanks and piping. Avoid iron, aluminum, or copper, as these can cause coagulation. - Cleaning
Immediately rinse tools and equipment with water after use to prevent resin buildup.
Impact of Storage Conditions on
PVDC Latex Properties
Storage temperature significantly affects the physical properties of PVDC Latex. Ensure that it is stored between 3–30℃ to maintain quality:
- pH and Chlorine Ion Concentration
Higher temperatures can increase pH and Cl-ion concentration. - Viscosity
Decreases at higher temperatures. - Surface Tension
Generally increases with higher storage temperatures. - Barrier Properties and Transparency
Higher temperatures can reduce barrier effectiveness and transparency, sometimes causing a yellow or reddish tint. - Latex Condition
Frozen latex will not regain its original properties after thawing. Exposure to high temperatures may also lead to coagulation. Even when latex is stored within the recommended temperature range of 3–30℃, its quality cannot be guaranteed beyond the specified shelf life.
Optimizing Coating Processes for
PVDC Latex
For the best results when applying PVDC Latex coatings, careful selection of materials and precision in processing are essential. Here are vital considerations to ensure optimal adhesion, uniformity, and performance:
Substrate Selection
- Film Compatibility
Choose substrate films that can endure the drying process, typically at temperatures above 100℃. - Uniform Thickness
Ensure the film has consistent thickness for an even coating application. - Avoid Antistatic Agents
Antistatic agents in the substrate can interfere with coating adhesion, resulting in irregular coating quality. Use antistatic-free films to maximize coating effectiveness.
Surface Preparation
- Corona Treatment
This step is recommended to enhance the bond between the substrate and the PVDC Latex, especially when working with low-adhesion materials like OPP. Corona treatment improves surface energy, ensuring reliable adhesion.
Anchor Coat (Adhesive) Selection
- Choosing the Right Adhesive
An anchor coat, typically a polyurethane-based adhesive, is essential to bond PVDC Latex to the substrate. Conduct trial applications to confirm compatibility, as unsuitable adhesives can lead to color changes or adhesion issues.
Additives for Enhanced Performance
- Surface Smoothness and Anti-blocking
Incorporate additives like inorganic silica or organic wax to improve surface quality and prevent layers from sticking during winding. Be cautious with additive levels; overuse can affect barrier performance and clarity.
Dilution and Solids Adjustment
- Water Quality
When diluting PVDC Latex, use water with a hardness level below 300 ppm. Excessive hardness can cause coagulation, compromising the latex.
Drying and Aging
- Controlled Drying
Start drying at a lower temperature to prevent skin formation, then gradually increase it towards the end of the dryer. This helps form a smooth, continuous film. - Aging for Enhanced Barrier Performance
A post-coating heat treatment (aging) can significantly improve barrier properties. We recommend aging at elevated temperatures, such as 40℃ for 48 hours, to promote crystallization and optimize coating performance.
Wind-Up and Blocking Prevention
- Avoiding Inter-Layer Pressure
Control wind-up tension and inter-layer pressure in the rolled film to prevent blocking. Add anti-blocking agents as needed to ensure smooth handling.
Follow these guidelines to maximize the performance of PVDC Latex coatings and achieve superior barrier properties and product durability. For further support on coating processes or technical inquiries, please reach out to our team.
Resin
PVDC Resin
Solvent-Based PVDC Barrier Coating
PVDC Resin is a thermoplastic white powder primarily composed of PVDC. When dissolved in a solvent, it provides high barrier properties similar to PVDC Latex but with a thinner application. This makes it a highly efficient solution for creating high-performance coatings with less material.
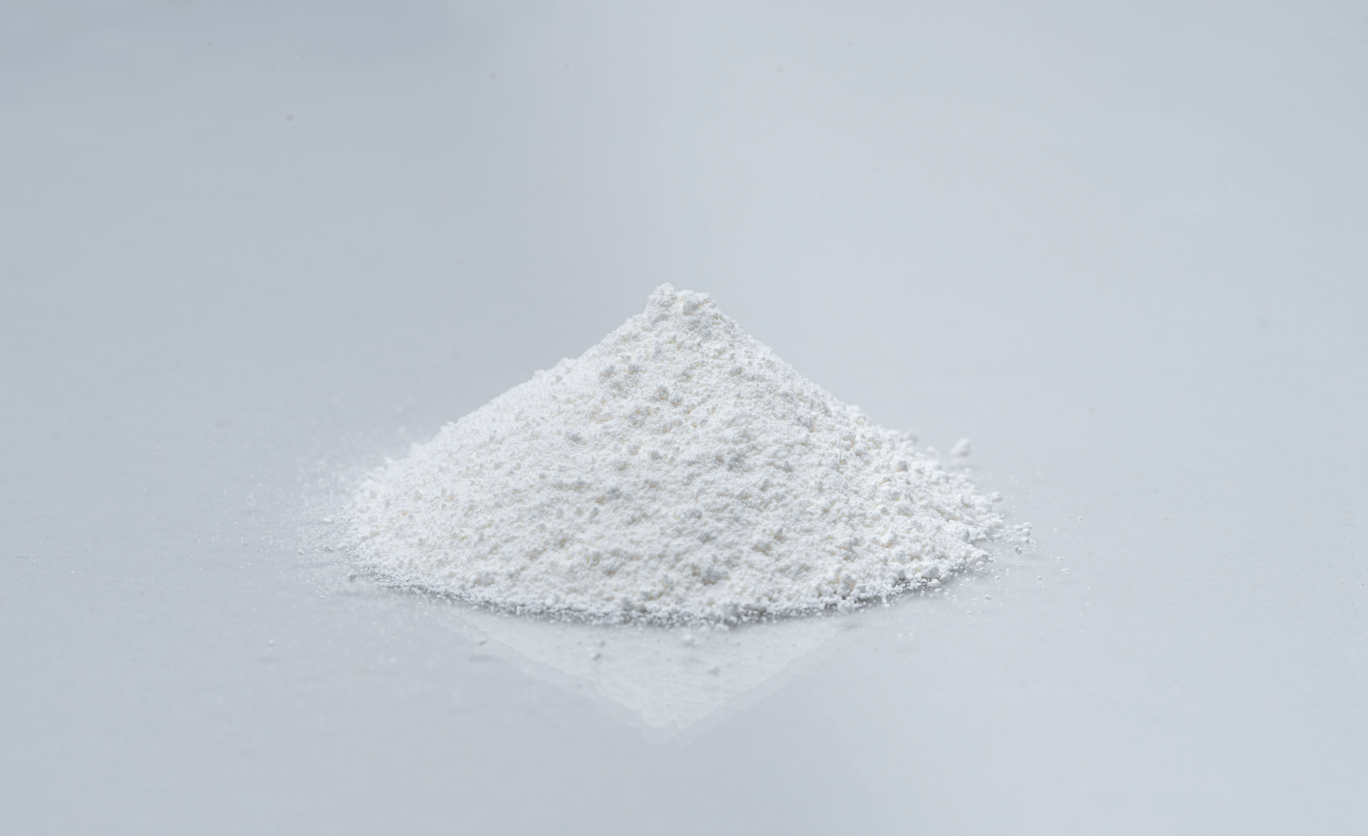