PVDC Resin Grades Overview
PVDC Barrier Coatings
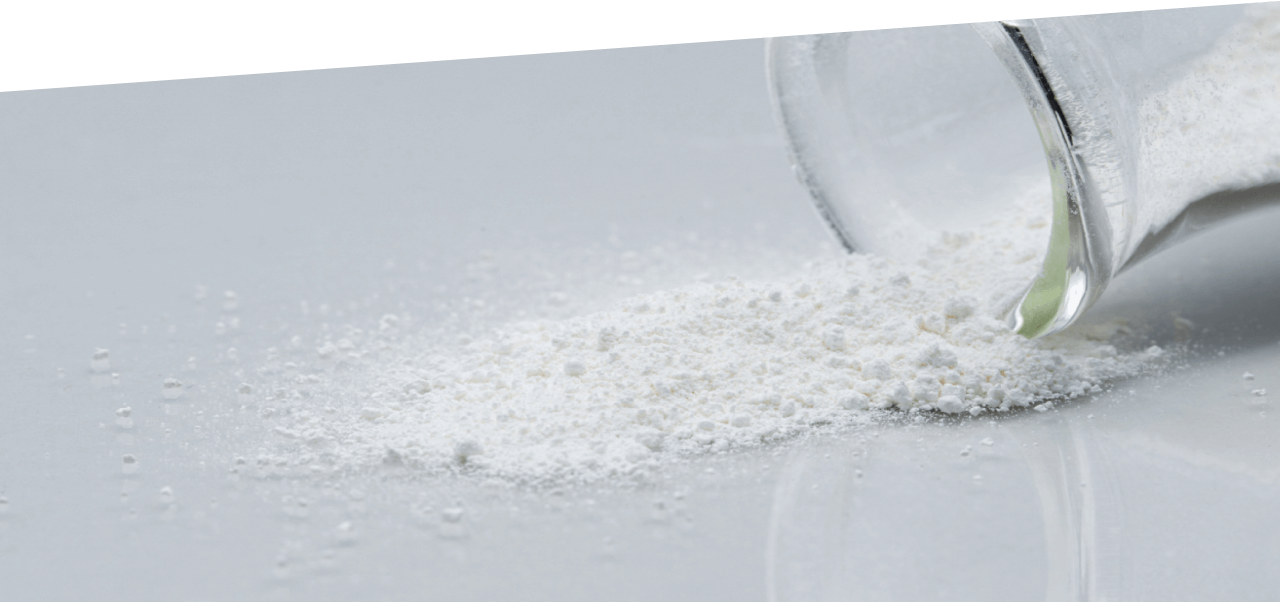
What is PVDC Resin?
PVDC Resin is a thermoplastic white powder composed primarily of polyvinylidene chloride (PVDC). When dissolved in an organic solvent and applied to substrates like films, PVDC Resin provides exceptional barrier properties similar to PVDC Latex. Its excellent water resistance also makes it suitable for cellophane coatings, offering versatile applications across various industries.
Key Properties of PVDC Resin
PVDC Resin offers a range of protective qualities essential for high-performance packaging:
- Oxygen Barrier: Reduces oxygen permeability, potentially extending product shelf life.
- Water Vapor Barrier: Helps prevent moisture intrusion, protecting sensitive contents.
- Heat Sealability: Supports the creation of strong, reliable seals during packaging.
- Fragrance Retention: Helps maintain product aromas, ideal for scented items.
- Oil & Chemical Resistance: Resists oils and chemicals, supporting package integrity.
- Flame Retardancy: Contributes to enhanced fire safety in various applications.
- Water Resistance: Suitable for humid environments, effective for cellophane and other substrates.
PVDC Resin Grades Overview
We offer a variety of PVDC Resin grades tailored for specific applications. These grades undergo rigorous aging processes (at 40℃ for 2 days) to achieve optimal performance in barrier properties.
Grade | Condition of Dissolving | Application | |||
---|---|---|---|---|---|
Solvent | Temperature for dissolving |
Water vapor transmission rate (g/m³・day) |
Oxygen transmission rate (cc/m²・day・0.1MPa) |
||
F310 | MEK | 20〜25℃ | 24 | 24 | Food Packaging and others |
F216 | THF/TOL=2/1 | 20℃ | 8 | 6 | |
MEK/TOL=2/1 | 70℃ | ||||
R204 | THF/TOL=2/1 | 50℃ | 2 | 3 |
TOL: Toluene
THF: Tetrahydrofuran
MEK: Methyl ethyl ketone
- Note:
・Water vapor transmission rate was measured by the AK-S LTX Method (S-059) (38℃, 90% RH) - ・Oxygen transmission rate was measured by AK-S LTX Method (S-079) at 23℃, Dry
- ・PVDC Latex-Coated Film converted to reflect 3μm PVDC Layer Thickness
- ・Water vapor transmission rate was measured by coating an ONy substrate, and oxygen transmission rate was measured by coating an OPP substrate.
- ・The values provided here are typical averages based on laboratory testing and should not be considered product specifications.
- ・These measurements were conducted using our in-house AK-S LTX Method. These examples are not guaranteed.
- ・Not all grades are compliant with regulations in every country or region, and some grades may be discontinued without prior notice. For regulatory details, please contact us directly.
Comprehensive Safety Data Sheets (SDS), technical specifications, usage guidelines, and regulatory details are available upon request.
Not all grades are compliant with regulations in every country or region, and some grades may be discontinued without prior notice. For regulatory details, please contact us directly.
Packaging Options
Our PVDC Resin is securely packaged in Flexible Intermediate Bulk Containers (FIBC), each holding up to 600 kg. This format allows for safe handling and efficient transport. Don't hesitate to contact us for smaller packaging solutions to discuss custom options.
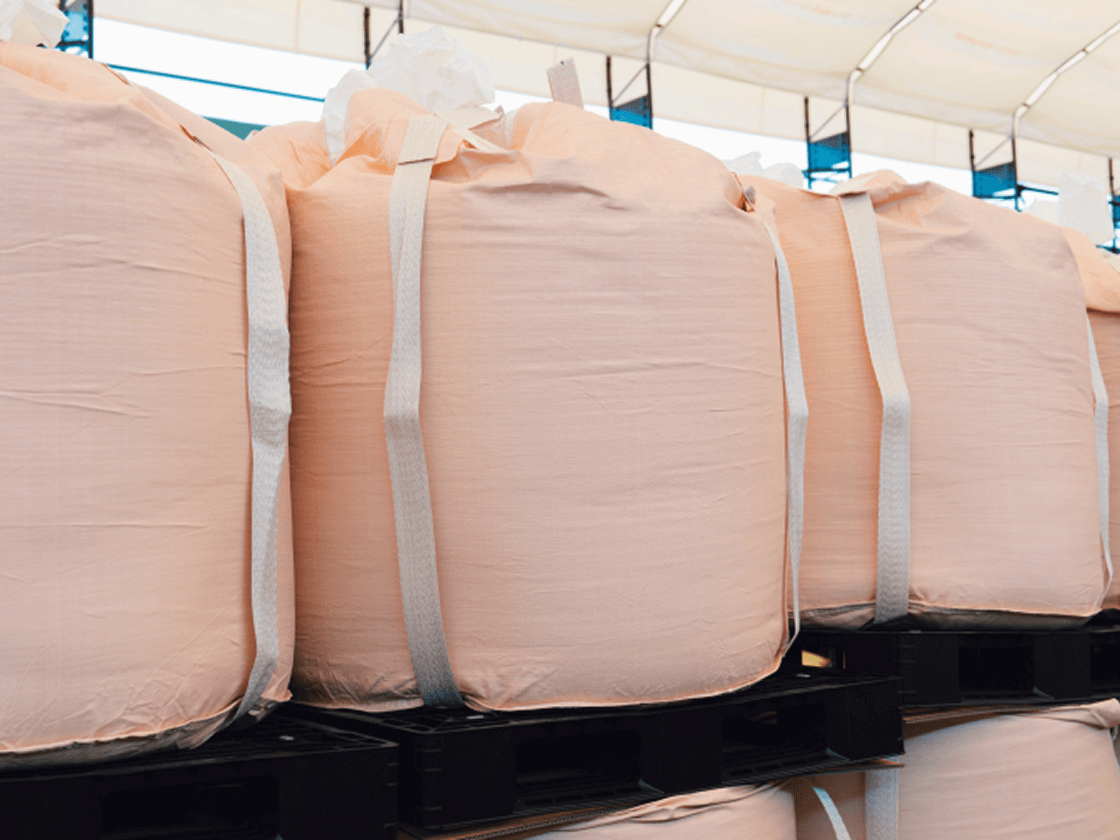
Packaging Example (600 kg)
Application Process for
PVDC Resin Coatings
Follow these steps for a strong, even coating:
① Dissolution
Gradually add PVDC Resin to a mixed solvent at room temperature while stirring. If heating, add the resin first, then increase to the desired temperature. Ensure any additives are introduced only after the resin has fully dissolved.
② Coating & Drying
Adjust dryer temperatures, starting low and increasing towards the end, to ensure complete solvent evaporation. Avoid high residual solvent levels within the film.
③ Wind-Up
Exercise caution with winding pressure to prevent blocking. Use suitable anti-blocking agents as needed.
④ Aging
For enhanced barrier and solvent resistance, age the coated film post-application. Typical aging conditions are 40℃ for 1–2 days. (Aging is not necessary for amorphous grades like F310.)
⑤ Additives
To optimize performance, additives such as slip agents for blocking prevention and adhesives for enhanced film adhesion may be used. Please contact us for further details.
Handling Precautions for PVDC Resin
Before Use: Always consult the specific SDS, wear protective equipment, and adhere to handling guidelines.
- Storage
Store below 30℃, away from UV and fluorescent lights. The resin slowly degrades at room temperature and can release hydrogen chloride gas which may lead to discoloration, especially at higher temperatures. Check the SDS for more details. - General Handling
Operate in a well-ventilated area, minimize dust, and wear protective masks, gloves, and eyewear to prevent inhalation or contact. Ensure proper grounding to avoid static discharge risks. - Mixing Additives
Conduct preliminary tests before use to confirm there are no adverse effects, such as viscosity changes, discoloration or other abnormalities. - Cleaning Equipment
Clean all tools and equipment immediately after use with a suitable solvent to prevent resin buildup. Exercise caution with solvents, taking safety and fire risks into account, and wear appropriate protective gear.
FAQ
PVDC Resin is a thermoplastic powder made from polyvinylidene chloride, used in solution coatings to provide high barrier properties.
It is commonly used to coat packaging films for food products, providing comparable performance to PVDC Latex.
PVDC Resin achieves the same protective properties with a lower amount of polymer, making it more efficient.
Yes, adhesives and other agents may be added to enhance specific properties, such as adhesion, antistatic, and lubricity.
Yes, post-application aging enhances the barrier effect and other properties, similar to PVDC Latex.
Latex
What is PVDC Latex?
PVDC Latex is an aqueous emulsion produced through the emulsion polymerization of vinylidene chloride (VDC). When used as a coating, it provides high resistance to water vapor and oxygen, along with heat sealability, chemical resistance, and flame retardancy. It’s an excellent choice for enhancing the protective performance of films or paper used in packaging applications.
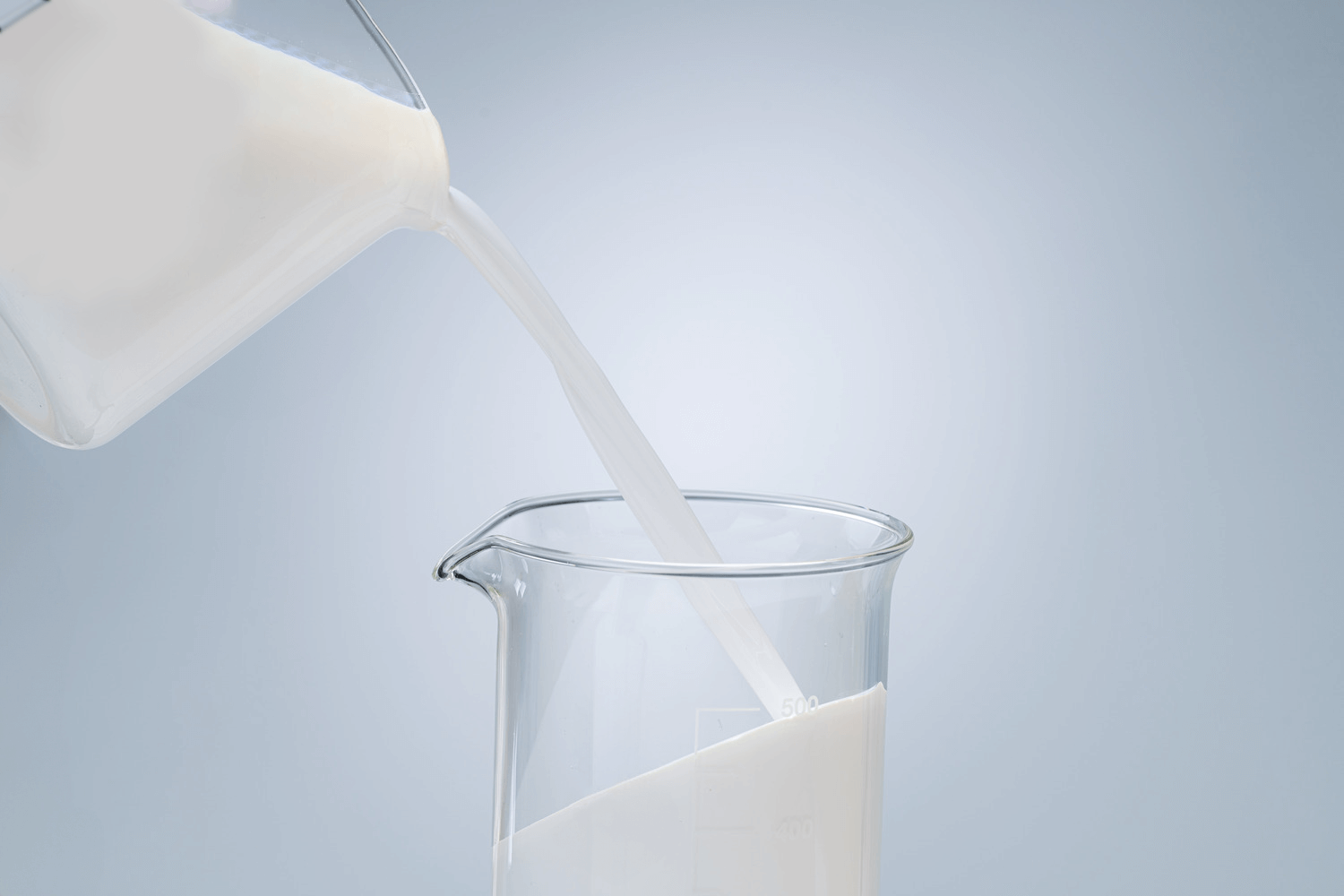
Sustainability Practices
At Asahi Kasei, we prioritize sustainability by offering solutions that protect products while reducing environmental impact.
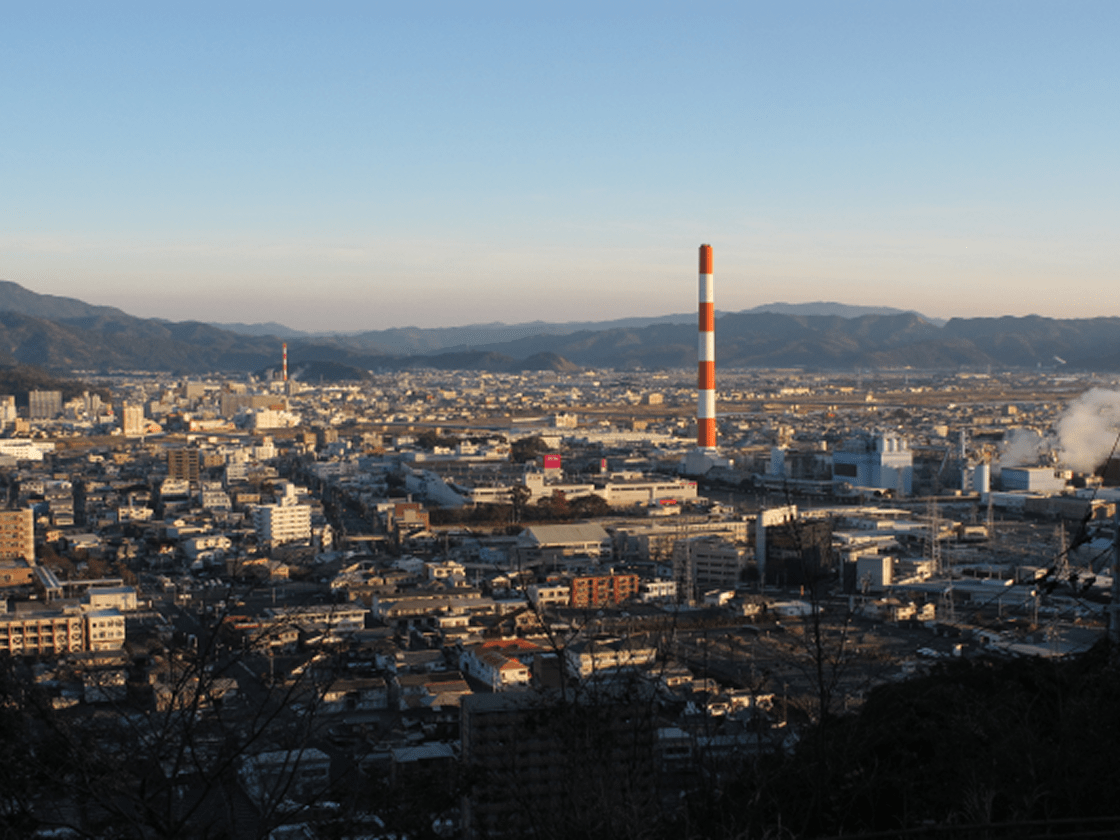